Interview with Philipp Schüll
Where are the headquarters of TRUMPF and what is its corporate purpose?
TRUMPF is a family-owned high-tech company based in Ditzingen near Stuttgart. TRUMPF now has 12,000 employees at over 70 locations worldwide. We offer manufacturing solutions in the fields of machine tools and laser technology. We are the market leader in flexible sheet metal processing and industrial lasers.
What career stages did you experience at TRUMPF?
I have been associated with TRUMPF for many years. As a student, I was here for an internship and I later wrote my bachelor thesis on industrial engineering here. I have worked for TRUMPF as an intern in China, as a lean management specialist in Ditzingen and England, and as a production manager in Switzerland. In addition, I was the advisor to the managing director for the machine tools and production sectors. During my time as an advisor, I achieved a master’s degree in production & operations management at the HECTOR School of KIT. The knowledge acquired there and the network at KIT's institute have assisted me in mastering the current professional challenges.
What challenges/changes is the TRUMPF Group currently facing?
Above all, I see challenges in an increasingly dynamic and complex world. Individualization in the field of production leads to custom production, and we have to react faster and faster. Our answer to this is “Industry 4.0”, digital transformation and agile working. This often concerns technological issues, for example algorithmics for artificial intelligence, big data or cyber-physical production systems. From my perspective, this approach is not enough. The changes for the individuals and the company are also of extreme importance - and, of course, new approaches. This is TRUMPF’s concept, as well.
Why focus on the "human" challenge?
A human being must acquire new skills. These are often less "digital" than one might expect, i.e., purely technical. Of course, knowledge must be given in the field of big data, for example, but it is more about changing the manner in which one thinks and behaves. This means cross-departmental collaboration, higher agility in projects or even virtual collaboration.
Why focus on the "organization" challenge?
Organizations are becoming more complex, and many topics can only be solved in an interdisciplinary manner. In our current projects, we need, on average, the skills of colleagues from five different departments, with a maximum of up to fourteen departments. For this purpose, today's forms of organization are not yet ready. They are rather functionally-oriented, although the challenges which we have today are "horizontal". New organizational forms need to be installed to be faster and more effective.
Why focus on the "new approaches" challenge?
In Germany, we are driven by technology and perfection, which is a big plus for the German economy. However, sometimes we forget to ask our customers what they really want, where they see added value, and what they are ultimately willing to pay for. We overload our products with features and only put them on the market when they are "perfect". The digital world ticks differently; there are so-called minimal viable products, that is, products that are just barely surviving. These provide the customer with a first added value, and they can give feedback on further improvements or additionally desired functionalities. The product development is completely based on customer benefit.
In summary: what does digital transformation mean for TRUMPF?
All in all, digital transformation is a massive project of change. It affects all areas of a company and thus also TRUMPF in its entirety. This, too, became very clear to me during my master studies at the HECTOR School. Our challenge at TRUMPF is to help 12,000 employees understand digital transformation. It's important to understand why a record-breaking company needs to start transforming right now and adding value to each and every employee. And it's important to help employees build skills and qualifications and bring the right experts together.
What will the corporate culture at TRUMPF look like?
At TRUMPF, we have two big advantages. TRUMPF as a family business is independent in its decisions and independent of external investors. TRUMPF guarantees innovation.
What advantage does the family-owned company TRUMPF have?
Another advantage is that there is long-term thinking: that I was facilitated in achieving a master's degree in production & operations management is just one example. This foresight also makes it possible to shape the digital transformation of products, processes, and methods in the long term and in the interest of the employees.
What is your job as Head of the Digital Transformation Program Office and what exactly do you do?
In my role as Head of the Digital Transformation Program Office, I support management in the development and implementation of our digital strategy. I accompany the implementation of strategic fields of action and I accompany change management.
What objective does TRUMPF want to achieve in 5 years?
Our goal is to be the digital leader in our industry in 5 years. An exciting task, considering that we are at home in the fields of machine tools and laser manufacturing.
What needs to be considered when implementing the digital transformation?
Basically, the digital transformation must be driven by management. This topic cannot be addressed "just" on the side. For this purpose, TRUMPF has created the post of Chief Digital Officer in the Group Management Board. In implementing the digital transformation, we must actively take our employees along and drive the project work forward. The program office I lead supervises 30 projects. Its mission is to track their progress and to support the project teams in their work.
Which measures are you referring to specifically?
The goal is for all TRUMPF employees to understand what the digital strategy is and why we need digitization. Communication, conviction and qualification are the buzzwords. We are planning an in-house platform where we can blog and discuss employees. In addition, we want to offer new learning formats there. We work very closely with our communications and HR departments.
What knowledge and skills did you acquire/deepen during the POM master’s program at the HECTOR School?
The network which I acquired at the HECTOR School supports me in all the tasks I am currently faced with. I learned a lot from others during my master’s in production & operations management. I have also learned to think outside the box and constantly question my own ways of thinking. It was very helpful that all my fellow students worked for successful smaller or larger companies, too. The lectures in multi-project management as well as in production systems and principles thoroughly prepared me for my current job.
How did you feel about the multicultural project and study work? What was the content of this work?
The multicultural project and study work was a great experience. The challenges and, above all, the enrichment created by the different views of international fellow students excited me. In the field of production systems, for example, we looked at how production principles and methods will change due to Industry 4.0. We thereby researched possibilities for improvement for clocked flow assemblies.
What do you see as the main advantages of the master's program Production and Logistics Management for you personally, but also for other graduates regarding Industry 4.0?
All in all, I found that I was able to internalize the theoretical content of my master's program much better than was the case in my undergraduate studies. There are three reasons for this:
• First, the quality of teaching and the discussion style.
• Secondly, interconnected thinking: I was able to harmonize the theoretical aspects well with my experiences and take the new findings directly to TRUMPF.
• And thirdly, the constant exchange and discussion with outstanding professors and fellow students. This topic is also very rewarding for TRUMPF. There have been concrete projects – among others with the support of the Institute for Production Technology wbk and the Institute for Material Handling and Logistics Systems ifl.
Is there anything else that you consider important for the video viewers in this context? (and that they should learn)
Even today, I am still in frequent contact with the Hector School, the wbk and the ifl. The master's program has created a reliable network from which we all benefit.
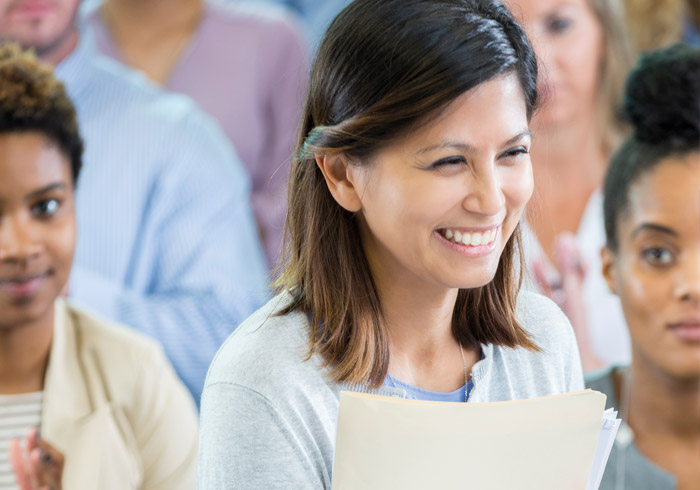
Our six M.Sc. programs combine cutting-edge technology and management expertise. Designed in close cooperation with the industry, they are a perfect match for ambitious engineers, computer scientists, and economists.
Read more
Read through interviews & voices of our HECTOR School alumni on why HECTOR School is unique, and how it fostered their careers.
Find out more